Praticamente tudo o que é construído no mundo necessita de um componente principal: o cimento. Talvez você não tenha parado para pensar o tamanho da importância do nosso protagonista das construções e o intuito hoje é mostrar um pouco da história e do processo de fabricação, citando alguns tipos comerciais mais comuns.
Nas construções antigas, como na Roma, Grécia e no antigo Egito, já se utilizavam misturas de solo de origem vulcânica com calcário e/ou gesso. Porém, voltando a 1824, após algumas tentativas de engenheiros e construtores de se encontrar um aglomerante durável e resistente, foi Joseph Aspdin quem obteve sucesso na descoberta, patenteando-a como Cimento Portland. A ideia original era misturar argila úmida e calcário e moê-los até se transformarem em um pó muito fino que, posteriormente, seria seco em vapor ou exposto ao sol e enfim levado ao forno sob altas temperaturas para calcinação, formação do clínquer e nova moagem. O resultado final era um aglomerante que endurecia rapidamente na presença de água.
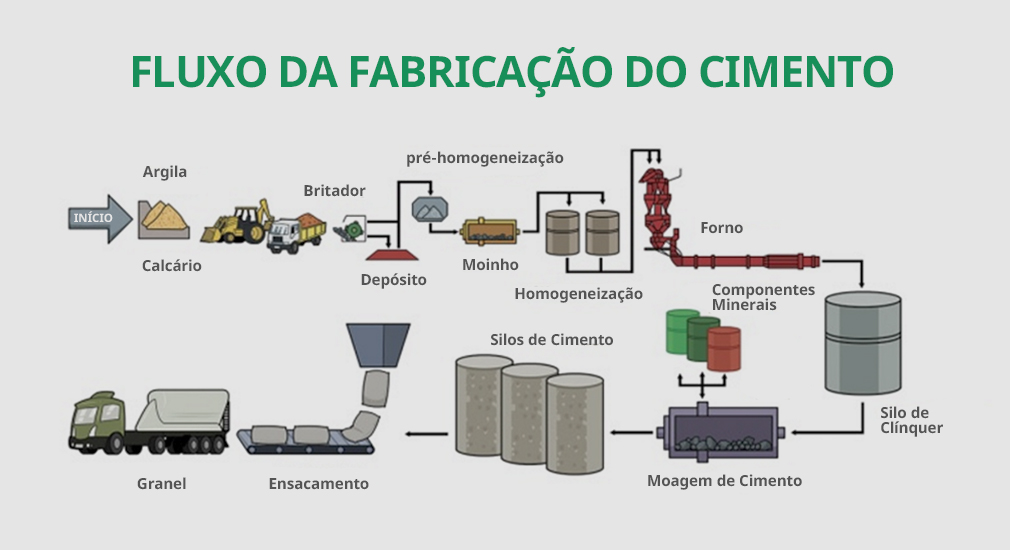
cimento, Na verdade, o processo é quase o mesmo até hoje, exceto pela adição de gesso, em cerca de 3% da massa do produto, a fim de aumentar o tempo de endurecimento da mistura do cimento com a água, o que denominamos como “tempo de pega”. O gesso é adicionado em etapa posterior, quando já foi obtido e moído o clínquer, produzindo o primeiro tipo: o CP I. Logo após, podem ser adicionados outros produtos, para produzir os mais variados tipos de cimento.
Em primeiro lugar, aparece o CP II-E, o mais utilizado na construção civil, composto de aproximadamente 60 a 90% da mistura gesso + clínquer e 10 a 40% de escória de alto-forno – que é o descarte da indústria siderúrgica, mas tem a função de aumentar a durabilidade do cimento e proporcionar uma resistência maior aos sulfatos. O segundo da mesma família, o CP II-Z, utiliza materiais pozolânicos provenientes de cinzas (vulcânicas ou da queima de carvão mineral) ou, ainda, produzidos artificialmente – ricos em sílica – que são utilizados principalmente em barragens e locais onde se deve garantir a impermeabilidade e estanqueidade da superfície. E o último, o CP II-F, é o cimento com adição de materiais carbonáticos, a fim de melhorar o preenchimento dos vazios na pasta endurecida.
Os demais tipos de cimento são o CP III (com maior teor de escória, de 35% a 60%), o CP IV (com 15 a 50% de pozolanas) e o CP V-ARI (Alta Resistência Inicial). Este último é o mais utilizado em obras maiores, principalmente por adquirirem resistência inicial (aos 7 dias) superior aos demais, agilizando o processo construtivo, e podem produzir concretos de alto desempenho e resistência aos 28 dias, dependendo das proporções utilizadas com a areia, a brita, água e outros aditivos.
Nas obras maiores, utilizamos o concreto prescrito em projeto, que é solicitado à concreteira, transportado pelos caminhões betoneira e lançado nas peças estruturais já montadas e dispostas para receber o produto. No entanto, em obras residenciais simples, é comum utilizar o concreto feito a partir mistura manual de areia, brita, água e cimento do tipo CP II em proporções (traço) de 1 (uma) parte de cimento, para 2 (duas) de areia e 3 (três) de brita – o famoso 1:2:3.
É interessante entender como utilizamos o cimento na Construção Civil, como foi descoberta e sua evolução ao longo do tempo. Pode ser que você já tenha estudado sobre o assunto ou, se não, tenha ficado em dúvida de qual escolher na hora de comprar. No geral, quem escolhe é o próprio engenheiro de execução, mas se você, cliente, estiver acompanhando, verifique o estado de conservação, pesquise sobre os materiais empregados na construção, a forma armazenamento e manuseio dos produtos (não só do cimento) para evitar desperdícios e gastos desnecessários na sua obra.
Fontes: Associação Brasileira do Cimento Portland (ABCP), Cimento Mauá, Cimento Itambé, Cimento Verde do Brasil.
Os comentários estão fechados, mas trackbacks E pingbacks estão abertos.